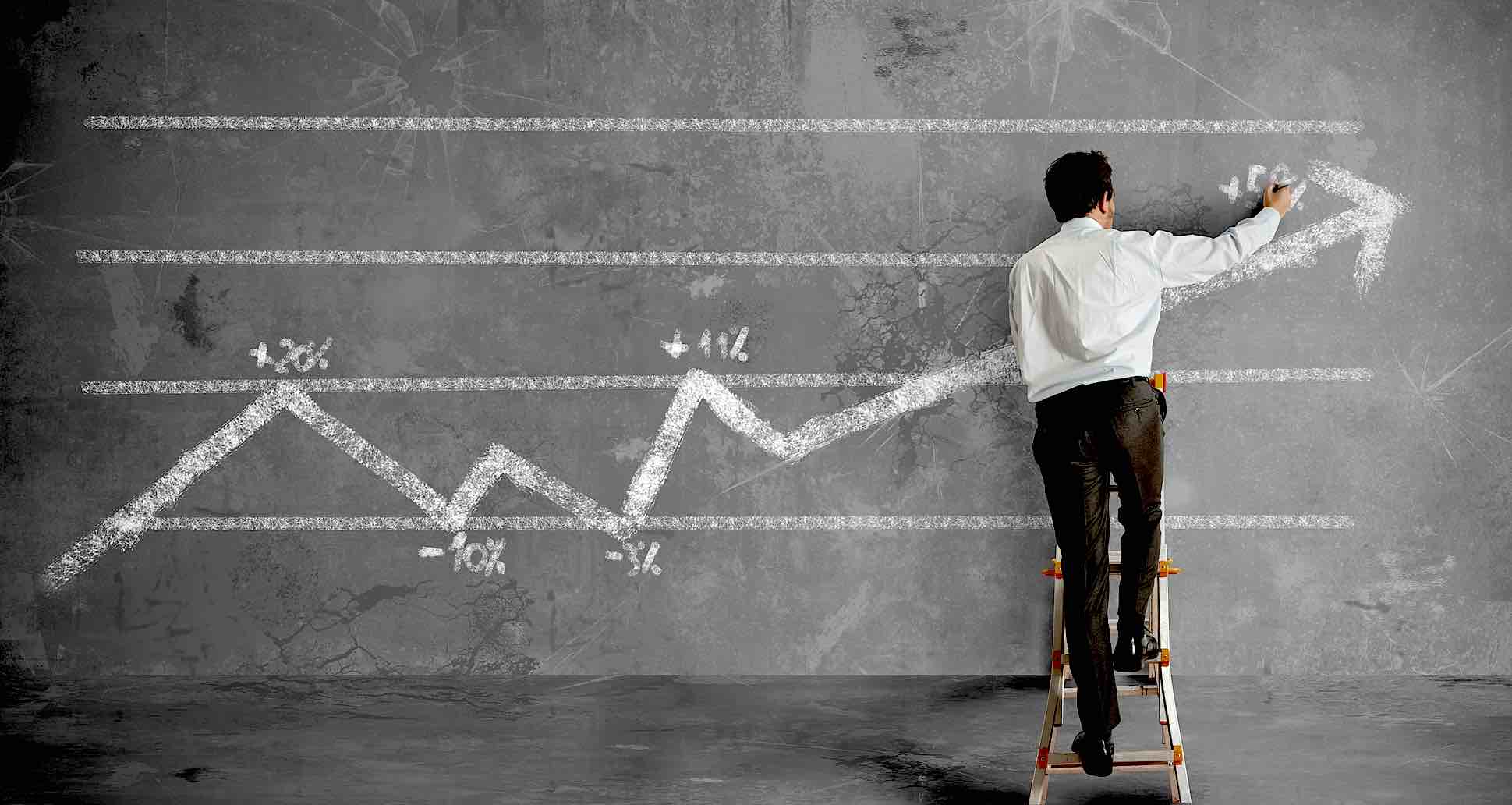
The principals of Operational excellence heavily focused on key elements such as Service, Quality, Cost, Revenue and Satisfaction.
We believe that real operational excellence is accomplished when improvements are sustained for a long time while continuous improvement is implanted throughout all levels of the organization.
Our approach is not limited to traditional “Lean” management techniques and 6 Sigma analysis. There are varies methodologies and procedures that we follow to achieve our objectives.
Our approach hubs around 3 essential areas that will lead to high performance.
In order to ensure high performance in an operation, it is required that above 3 fundamentals are interlinked with each other.
Frameworks are important to make sure your operation is doing the right things in the right way. For example, you cannot be pro-active about the consumption of your resource unless you have a robust framework for Forecasting and Planning. We can support you to build a Target Operating Model (TOM), restructure your organization and establish meaningful Management Information.
Processes are what your staff do to fulfil your operational needs. It can be answering customer enquiries, maintaining an account, responding to a complaint or scanning the mail. Lean Consulting can help ensure that every process is designed to maximize efficiency and productivity.
People deal with how you manage staff. Managing poor performance, behavioral issues, rewarding high performance, coaching and development of staff are the focus of this area. Managers are often the least trained people in the organization. Lean Consulting can help correct this and ensure your operation is ready for a culture of continuous improvement.